By Scott Zahn
Recent data released by the Bureau of Labor Statistics tells us that the national unemployment rate continues to drop but, at 7.9% as of September, remains high. Data, however, can sometimes be misleading, and for companies struggling to find workers for their warehouses or distribution centers, these current unemployment numbers represent good news and not-so-good news.
First the good news: there is a large available talent pool eager to go to work. The not so good news? Available workforce doesn’t always mean a qualified workforce.
Only a small percentage of the 12,600,000 currently unemployed have the physical skills, willingness and aptitude to work in a warehouse environment. Former retail or hospitality workers, who represent a large number of the unemployed due to the coronavirus, may not have the stamina for warehouse product picking using traditional technology that typically involves holding a bar code scanner in one hand while reaching for and lifting products with the other hand. Using one hand instead of two to lift heavy objects is difficult and can frequently cause debilitating back strain.
An alternative to traditional hand-held scanners involves voice-enabled technology for warehouse picking, where workers receive easy-to-understand voice prompts from a headset to direct them to picking locations and instruct them in picking tasks.
Voice-enabled picking—also known as Hands-Free, Eyes-Free™ picking because workers don’t have to glance down to read and scan bar codes—is not only faster and more accurate than other workflows, it is also less physically demanding because workers have two hands to do the lifting instead of one. There is also less back strain compared to reaching for and lifting boxes with one hand while also holding a scanner or a sheet of paper. Hands-Free, Eyes-Free voice-picking technology allows workers to keep their heads up and eyes alert, an important safety benefit in an active and sometimes dangerous warehouse environment.
Possibly the best reason hiring managers can be excited about voice-optimized picking is that the largest portion of the available workforce—millennials and members of Generation Z—absolutely love voice-enabled everything. They were essentially born using voice-directed devices for everything in their lives. More so than any generation before them, much of the available workforce are pros at two-way communication using voice commands as they witnessed the explosive growth of smartphones, earbuds and Bluetooth, along with voice-activated digital voice assistants like Alexa and Siri. These and other examples of voice-enabled artificial intelligence are increasingly integral to daily life.
Because voice interaction tends to fit nicely with their lifestyle, this groups tends to seek out, apply for and stay at jobs with this technology. They may even perform at a higher level in jobs that feature two-way voice interaction.
The bottom line is, for the largest segment of today’s available workers for warehouse and distribution center environments, putting on a headset is like putting on a uniform—and their game face! Hiring managers inside the supply chain and logistics industries would do well to mirror inside their warehouses and distribution centers the voice-centric technology that is so appealing to much of today’s available workforce.
About the Author
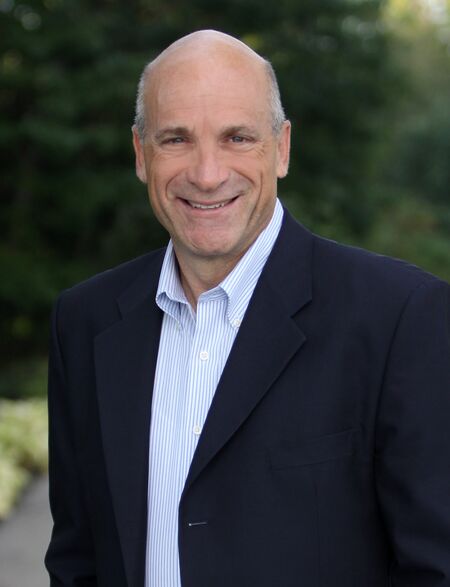
Scott Zahn is a warehouse productivity advisor for wholesalers, manufacturers, third-party logistics and self-distributing retail operations. He has worked for the past four years as a productivity advisor for Mountain Leverage, a Honeywell Total Solutions Partner, implementing a variety of warehouse voice picking systems to reduce the costs associated with fulfillment operations. Zahn can be reached at szahn@mountainleverage.com.