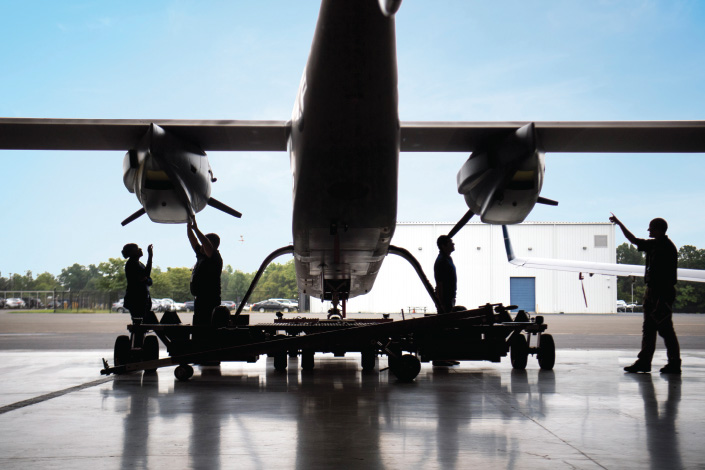
West Virginia’s Defense Manufacturing and Maintenance Companies
By Samantha Cart
A commitment to service and a sense of patriotism are often byproducts of living in West Virginia. Mountaineers are loyal and selfless, and it is no surprise that these values draw in defense industry companies dedicated to creating and maintaining apparatus for the U.S. military and its allies.
Some of the biggest names in defense retain top-tier facilities on Mountain State soil, a little-known fact that may surprise some. Whether it is Northrop Grumman’s Allegany Ballistics Laboratory manufacturing tactical rocket motors or Pratt & Whitney repairing an aircraft engine damaged in combat, these powerhouse companies have a significant impact on West Virginia and the nation in terms of security and economy.
Aurora Flight Sciences
Some brands have made an indelible mark on the public consciousness, and Boeing—the world’s largest aerospace company—is certainly one. Aurora Flight Sciences, a Boeing Company, works on the cutting edge of aircraft technology from its advanced manufacturing facility in Bridgeport, WV.
For the defense industry in particular, Aurora delivers high-quality composite, metal and structural components used on military unmanned aerial vehicles and helicopters and innovates new aircraft configurations, propulsion technologies and autonomous systems for use in future aircraft.
“Aurora designs, builds and flies aircraft and enabling technologies that have never been done before,” says Vice President of Manufacturing Eric Thompson. “Whether it is a new robotic manufacturing system to produce quality aircraft parts at lower costs or a cutting-edge X-plane to advance novel concepts from idea to flight, Aurora’s daily operations are the definition of unique.”
In the Mountain State, Aurora manufactures composite structures for MQ-25, aft fuselage, nacelle and v-tail assemblies for Global Hawk and Triton and nacelles and main rotor pylons for military helicopters. Its manufacturing processes range in scope from laying up carbon fiber composite components by hand to fully automated robotic machining, transport and inspection technology.
According to Thompson, Aurora is proud of its long-term support of defense industry programs. The company first delivered v-tail assemblies for the Global Hawk program in 1995, and its role in the program has continued to expand ever since.
“Over the years, we have worked on many programs under the Defense Advanced Research Projects Agency, from a line of unmanned vertical takeoff and landing vehicles in 2003 to today’s early-stage development programs in artificial intelligence,” he says.
Aurora has experienced growth in West Virginia and nationally since its founding in 1989, and the company continues to take on new and exciting opportunities.
“We are particularly excited about beginning work on building two next-generation motherships for Virgin Galactic and continuing to support our troops with growing U.S. Department of Defense (DOD) programs and next-generation platforms,” Thompson says.
Azimuth Incorporated
For more than 30 years, Azimuth Incorporated, a Morgantown-based company, has been supporting the DOD with its specialization in the design and manufacture of military-grade hardware and software for use on land and in maritime environments.
Azimuth specializes in software and electronics engineering, rapid prototyping, manufacturing, geographic information system/infrastructure analysis and biometrics and has developed numerous products for government and commercial customers, including marine integrated bridge systems, rugged digital video recorders (DVR), biometric enrollment systems, diver tracking systems and logistical support systems.
“Many of our systems are unique in nature, and we are known for designing and manufacturing very rugged systems that can withstand high shock, severe temperatures and vibration,” says President and CEO Craig Hartzell.
Just one example of Azimuth’s innovation is its Rugged High Definition-Mission Data Recorder (HD-MDR). Rigorously tested against high-speed military combatant craft, this product provides sea, land and air systems with a powerful computing system that can operate as a stand-alone MDR or as a part of a larger system to fill the need for quality,
reliable, rugged missions video requirements. The HD-MDR integrates a multi-channel DVR with platform meta-data
logging capability to implement a highly capable all-in-one mission data recorder.
Enjoying a steady growth since its inception in 1988, Azimuth is an ISO certified company and is considered a compliant exporter by the International Traffic in Arms Regulations and the U.S. Department of Commerce’s Export Administration Regulations. The company has received a number of honors and awards, including the National Small Business Administration District Director Award and Veteran Small Business Advocate of the Year. It was also named an Inc. 500 Corporation.
Hartzell, along with many of Azimuth’s other team members, is a veteran, which adds another dimension of passion to the company’s work.
“Most of our staff have a family connection with our great military, and all of our staff consider themselves patriots,” he says. “We are driven to support the defense of our nation and its allies. I made a commitment to our engineering group and staff that we will only pursue work worth doing, and our support of the DOD lives up to that promise.”
CFOAM LLC
On the surface, CFOAM LLC’s operation may seem simple—the company makes its trademarked CFOAM carbon foam from coal. A novice might wonder what coal has to do with the defense industry, and the answer delves into the fascinating uses for the diverse product.
“CFOAM is used to produce a very unique material that displays a number of amazing characteristics,” says General Manager Rudy Olson. “Carbon foam can withstand temperatures of over 5,000 degrees Fahrenheit without melting, and because it is electrically conductive, it can shield electromagnetic radiation. CFOAM is also highly fire resistant, can be designed to absorb energy from an explosion or projectile, absorbs radar, can be coated with a variety of materials to create composite structures and can withstand the toughest environmental conditions.”
In regard to the defense industry, CFOAM is currently manufactured commercially to produce tooling used to make carbon fiber composite parts for the production of certain military aircraft, and CFOAM LLC is currently manufacturing components that are being used in the development of products for a variety of military applications.
What makes CFOAM so unique is that it is not a polymer, ceramic or metal.
“In many ways it falls between all of these common materials, giving it a unique combination of material properties,” says Olson. “These include being very lightweight, high strength, easy machinability, low coefficient of thermal expansion and good thermal stability at high temperatures. It can be used as an electrical insulator, electrical conductor, thermal insulator or thermal conductor.”
CFOAM LLC was founded in 2016 and was recently purchased by CONSOL Energy. The company’s customer base continues to grow both in the U.S. and internationally. In 2022, CFOAM LLC received seven export awards for the West Virginia Governor’s Commendation for International Market Entry.
Its reputation for innovation and success has allowed leadership to create valuable partnerships with other U.S. companies involved in creating products for the military, including Advanced Carbon Products Technologies and American Maglev Technologies.
“We have discovered that building good relationships enhances our chances of success when solving difficult problems for the military,” says Olson.
FCX Systems
FCX Systems is the world’s leading manufacturer of solid-state frequency converters, ground power support and custom power conversion solutions for military, commercial, shore power and industrial applications around the world. Based in Morgantown, WV, the company has been developing its products for more than 35 years.
“We design and manufacture power units that allow airplanes to plug into power on the ground for testing and maintenance purposes,” says CEO Craig Walker. “The great majority, around 90%, is for military use—the U.S. and its allies—in hangars, mobile units and ships. Without our units, these planes would operate only with their auxiliary power units, which is more costly.”
There are only five companies in the U.S. that manufacture ground power units, which situates FCX in a unique niche market. FCX frequency converters and diesel ground power units have been installed in more than 80 countries and on every continent. Industry leaders such as Northrop Grumman, Boeing and Lockheed Martin; major airlines and international airports; and U.S. and foreign militaries rely on FCX Systems for durable products that perform beyond the required operations.
The Morgantown facility is FCX’s sole location. FCX engineers design each unit, and while the magnetics and enclosures are outsourced, the West Virginia team does all the wiring and manufacturing and tests each unit against military specifications.
FCX Systems was awarded the President’s “E” Award for exporting excellence in 1999 and the President’s “E” Star Award in 2016, the highest recognition for a U.S. company engaged in exporting. It was the first company in West Virginia to receive this honor.
Lockheed Martin
From the outside looking in, it seems Lockheed Martin does it all. From autonomy and artificial intelligence and electronic warfare to advanced manufacturing and integrated air and missile defense, the company builds products to support U.S. warfighters and U.S. allies around the world.
“What Lockheed Martin does is important to us all,” says Chuck Saffle, site manager for Lockheed Martin’s sub-assembly plant in Clarksburg, WV. “We provide our military men and women with the solutions they need to defend our nation, as well as the technologies we all use every day. Here in Clarksburg, we have been fortunate to do our part since 1962, when the plant produced its first aircraft component.”
At the Clarksburg location, which falls under the company’s aeronautics division, the Lockheed team builds and assembles components that feed into the C130J Hercules, the longest running military aircraft production line in history. With thousands of square feet of manufacturing and warehouse space, Lockheed’s West Virginia team produces C130J parts such as the cargo ramp, landing gear doors, side panels and center wing beams. The skilled labor required to make these parts is a testament to the team’s skill and passion.
“At our facility, we kit parts delivered to us from vendors across the U.S. and load them into floor-mounted assembly fixtures,” says Saffle. “From that point, we complete the process using tight tolerances and specifications and then ship the finished product to our main plant in Marietta, GA, for final installation. At Lockheed Martin, we’re a family, and we take honor and pride in providing quality, safe, efficient products to our military personnel.”
While Lockheed is a global company, its West Virginia facility has seen steady growth over the past several years. The company hires new employees nearly every year and supports an annual build rate between 20 and 36 aircraft.
Northrop Grumman
Northrop Grumman designs, develops, builds and supports some of the world’s most advanced aircraft, spacecraft, cyber security systems and radars from numerous facilities across the globe. At the company’s Allegany Ballistics Laboratory (ABL) in Rocket Center, WV, employees help design, develop and manufacture tactical rocket motors, medium caliber ammunition, composite components and end items and fuze and electronics equipment. The highly skilled team also supports national security efforts by developing and building defense systems for DOD customers and U.S. allies.
Northrop Grumman at ABL is unique in that it is the only company in the defense industry to bring four key technologies—metals, electronics, composites and energetics—together on one campus.
“Northrop Grumman employs approximately 1,600 Ph.Ds., scientists, engineers, technicians and hourly workers who work side by side on integrated product teams solving problems in real time,” says Steven Weiss, ABL site lead and director of the tactical propulsion and ordnance operating unit for Northrop Grumman. “We produce thousands of precision parts each day ranging from tooling to medium and large caliber ammunition to motor cases for next-generation missiles.”
The ABL is made up of more than 1 million square feet of manufacturing space spread over 1,600 acres. It supports more than 100 competitively awarded production contracts that aid U.S. warfighters’ mission. The work performed at the ABL each day directly supports the warfighter’s edge and safety in the battlespace, according to Weiss. This includes products like the insensitive munitions rocket motors for the Guided Multiple Launch Rocket System program, which enhances safety and limits collateral damage, and the HELLFIRE Rocket Motor that propels HELLFIRE missiles. This part is currently used on dozens of platforms, including helicopters, unmanned aircraft, land combat vehicles and combat ships, across the world.
According to Weiss, manufacturing these components requires the ABL team to be in lock step with its customer base to produce exceptional products with an incredible breadth of capabilities in one place. This objective has kept the company on an upward trajectory for growth.
Earlier this year, Northrop Grumman announced the construction of a new, 113,000-square-foot facility in West Virginia that will increase its capacity with the defense industry and support long-term growth. The missile integration facility will be a factory of the future designed to meet increasing demand by investing in adaptable manufacturing techniques. It is scheduled to be completed in 2024, and, once finished, will be able to support 600 missile strikes per year.
Pratt & Whitney Engine Services
With aircraft engines used in both civil and military aviation, Pratt & Whitney is a well-known name. Pratt & Whitney
Engine Services in Bridgeport, WV, performs maintenance, repair and overhaul (MRO) for several models of Pratt & Whitney aircraft engines, including the iconic PT6A turboprop engine that powers the Texan II trainer aircraft—hundreds of which are in use throughout the U.S. military.
“The PT6A is also used to power certain tactical aircraft that the military relies upon for missions such as reconnaissance,” says Director Tim Tucker. “Additionally, the facility also services JT15D, PW300 and PW500 engines installed on military aircraft. I estimate that about 30% of our business is working on military engines.”
Once an engine reaches a certain number of hours of flight, it must be removed from the aircraft and shipped to a facility—like the one in Bridgeport—where the engine is completely disassembled and each part carefully examined, repaired or replaced as required.
“We then reassemble the engine and run it in our test cell to ensure that it performs up to our high standards when it is reinstalled on the aircraft,” says Tucker. “We made the engine—so no one can maintain it better than we can.”
This service is important to Pratt & Whitney’s defense customers because the availability of each aircraft is dependent on the reliability of the engine. By maintaining the engines to the highest original equipment manufacturer standards,
the Bridgeport facility plays a role in enabling the military to conduct missions as planned and in emergency situations.
“We view our operations as an integral part of the military’s mission supply chain. That is a responsibility that we take very seriously,” Tucker says.
The MRO shop in Bridgeport is supported by a global team of engineering and maintenance professionals, with field support managers around the world to help customers troubleshoot engine issues and mobile repair team technicians that can be at a customer’s location in a matter of hours and work quickly to restore an aircraft to flight.
Pratt & Whitney continues to grow specifically in West Virginia, where its workforce has grown 20% over the past few years. The company is currently investing $30 million into the Bridgeport facility to create MRO capability for the PW800 engine, which powers G500 and G600 business jets from Gulfstream and has been selected to power the G400 as well.
Protecting West Virginia
By Arianna Whitehair
Two major firearm manufacturers in the Mountain State, Wolfpack Armory and Foley Defense, are working to equip local law enforcement and the general public with the highest quality weapons to ensure they are safe and able to continue protecting our communities and their people.
Wolfpack Armory
Wolfpack Armory (WPA) is a small, family-owned and operated company based out of Fairmont, WV, that specializes in AR-15 manufacturing.
Highly committed to providing quality customer service, it provides top-quality firearms by developing new weapons technology and using the highest quality materials available on the market. With the mission of bringing military-grade, all-American firearms to anyone who leads, hunts or defends, WPA custom manufactures firearms and weapons for both hunting and defense applications and offers handguns, rifles, pistols and Glock slide machining services.
By working with materials like steel, aluminum and stainless steel, the company is able to provide law enforcement and military industries with the highest quality weapons. All firearms by WPA are backed by an unlimited lifetime warranty.
Foley Defense
Foley Defense is a full-service certified cerakote applicator, custom computerized numerical control, or CNC, machining and firearm manufacturer located in Shady Spring, WV. The company is dedicated to providing general customers and county and state law enforcement with quality firearm products and services that include but are not limited to laser engraving, suppressors and side milling. Passionate about providing top-shelf customization and products to clients, Foley operates a highly innovative, precision-based manufacturing facility where customer service is top priority. A type 07 FLL manufacturing company, Foley specializes in AR-15s and is focused on building high-end suppressors.
A relatively new and increasingly popular form of gun coating, cerakote is a polymer-ceramic composite coating that can be applied to metals, plastics, polymers and wood. Cerakote ceramic coatings are a common choice of coating, as they utilize state-of-the-art technology that outperforms any competitive coating in both laboratory settings and real-world applications. This unique formulation enhances a vast number of physical performance properties like abrasion and wear resistance, corrosion resistance, chemical resistance, impact strength and hardness. At Foley Defense, each one of these properties is rigorously tested to guarantee that cerakote products remain at the forefront of the ceramic coatings market.
Trained and certified in applying cerakote ceramic thin film coatings for firearms and other products that require both a durable and attractive finish, Foley uses modern chic manufacturing techniques along with fiber laser engraving to customize products quickly, efficiently and at affordable prices. It also offers knives, tools, eyewear, consumer electronics, wearables, industrial valves, sporting and athletic equipment, robotics, audio equipment and fresh and saltwater applications.
Making its start in the defense industry a little over eight years ago, Foley has seen its business nearly double in growth over the past two years and almost triple in growth this year, a trajectory it believes the business will continue on for years to come as people begin taking an increased interest in safety and personal protection measures.